Virus-associated Carcinogenesis
- Immunology, Infection and Cancer

Prof. Dr. Ralf Bartenschlager
Our division –established in March 2014– aims at deciphering the basic principles underlying tumor formation in the context of chronic viral infection. Our research centers on liver cancer, which is one of the most frequent causes of cancer-related deaths.
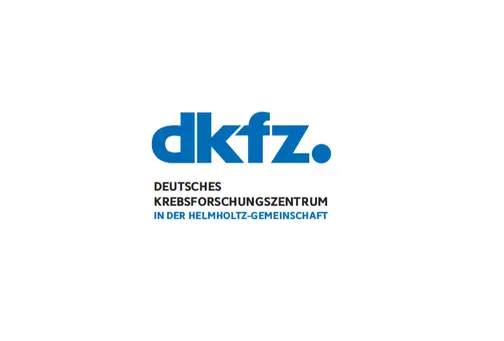
Our Research
Our division –established in March 2014– aims at deciphering the basic principles underlying tumor formation in the context of chronic viral infection. Our research centers on liver cancer, which is one of the most frequent causes of cancer-related deaths. Around 75% of all liver cancer cases are linked to infection with hepatitis B virus (HBV), Hepatitis D virus (HDV) or hepatitis C virus (HCV). Thus, liver cancer is a paradigm for infection-associated tumors. The medical relevance is very high as reflected by the high numbers of persistently infected individuals: 240 million in case of HBV, an estimated 10-20% being co-infected with HDV, and around 70 million in case of HCV. These people have a high risk to develop serious liver damage, most notably liver cirrhosis and hepatocellular carcinoma. Important comorbidity factors are metabolic syndrome, alcohol consumption and chronic inflammation as induced and sustained by persistent virus infection. Since therapy of liver tumors still is very inefficient, there is an urgent need for preventive and therapeutic regimens as well as more sensitive diagnostics.
Together with our sister department “Molecular Virology” at University Hospital Heidelberg we already laid the ground to study the basic principles of the replication cycles of HBV, HDV, HCV and related viruses. In addition, given the similarities in important cell biology aspects, we have integrated studies focusing on the replication cycle of the severe acute respiratory syndrome coronavirus-2 (SARS-CoV-2) with the ultimate goal to develop broadly active antiviral drugs to increase future pandemic preparedness. Building on this expertise, within the division “Virus-Associated Carcinogenesis” at the German Cancer Research Center our research is centered on the following main topics:
- The mechanisms how persistent hepatitis virus infections are established, how chronic infection contributes to the development of liver cancer and to devise novel concepts to break viral persistence, thus reducing the cancer risk
- The basic principles how virus infections are sensed, how viruses overcome these antiviral strategies and the role of cell-intrinsic antiviral signaling in tumor development and therapy
- The role of iron-regulatory networks in infection and inflammation-induced liver tumor Formation
- The establishment of a portfolio of oncolytic parvoviruses and the analysis of virus-host cell interactions associated with virus-induced cell disturbances
Detailed information about the research work in the individual research groups in our department can be found on their websites:
Group of Ralf Bartenschlager
Group of Marco Binder
Group of Jürg Nüesch
Group of Stefan Seitz
CoViPa research network
The following independent units belong to our department too:
Group of Stella Autenrieth
Group of Timo Bund
Group of Barbara Leuchs
Team
-
Prof. Dr. Ralf Bartenschlager
-
Alicia Avenhaus
-
Dr. Marco Binder
-
Dr. Sandra Bühler
-
Liubov Chuprikova
-
Aditi Dhawan
-
Marius Flörchinger
-
Veronika Frehtman
-
Anne-Charlotte Gerstenberg
-
Leon Hennecke
-
Doroteja Ilic
-
Barbara Leuchs
-
Prof. Dr. Martin Löchelt
-
Maria del Pilar Milla Picon
-
Dr. Giulia Mizzon
-
Kerstin Mohr
-
Dr. Catherine Moreau
Scientific Project Management
-
Marcus Müller
-
Dr. Firat Nebioglu
-
Dr. Jürg Nüesch
-
Gael Palais
-
Claudia Plotzky
-
Ilka Rebhan
-
Aleksandr Refeld
-
Viola Reuschenbach
-
Alexandre Roubenne
-
Theresa Schindler
Administration
-
Dr. Moritz Schüßler
-
Stefan Seitz
-
Carla Siebenkotten
-
Sebastian Stegmaier
-
Iken Strahl
-
Alina Stukan
-
Madelon van Hoek
-
Katrin Woll
-
Guandi Wu
-
Sandra Wüst
Scientific Project Management
-
Shangqing Yang
Selected Publications
Bonadonna M. et al.
Cortese M. et al.
Gillich N. et al.
Zander D. Y. et al.
Get in touch with us
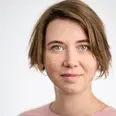
Dr. Catherine Moreau
Project Management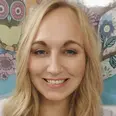
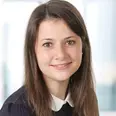